Reducing losses and increasing efficiency in production
At Iskraemeco, we believe that every step in the production process is important to our success. That is why we are constantly looking for new ways to improve our processes, reduce losses and increase efficiency. In this article, we present some of the most important improvements we have recently implemented in our production processes in Kranj.
Why is loss prevention important?
Every company generates different types of production losses. Each of these losses represents untapped potential and can have a negative impact on cost, product quality and customer satisfaction. There are eight basic types of loss, which can be summarized with the acronym TIMWOOD(S):
- Transport: unnecessary movement of materials and products.
- Inventory: excessive stocks of material and finished products.
- Motion: unnecessary movement of workers between workplaces.
- Waiting: waiting for materials, tools, instructions, or for the completion of previous processes.
- Overprocessing: unnecessary or duplicated processes in production.
- Overproduction: production of more products than can be sold.
- Defects: product defects during production.
- Skills: underutilized knowledge and experience of employees.
How has Iskraemeco tackled each type of loss?
At Iskraemeco, we believe that success is the result of teamwork. That is why we have involved all employees in the improvement process, ranging from production, engineering, operational excellence, IT and development to management. Together, we have identified the eight basic types of loss that have the most impact on our business and developed specific measures to reduce them. The results of these joint efforts are visible at every step of our production.

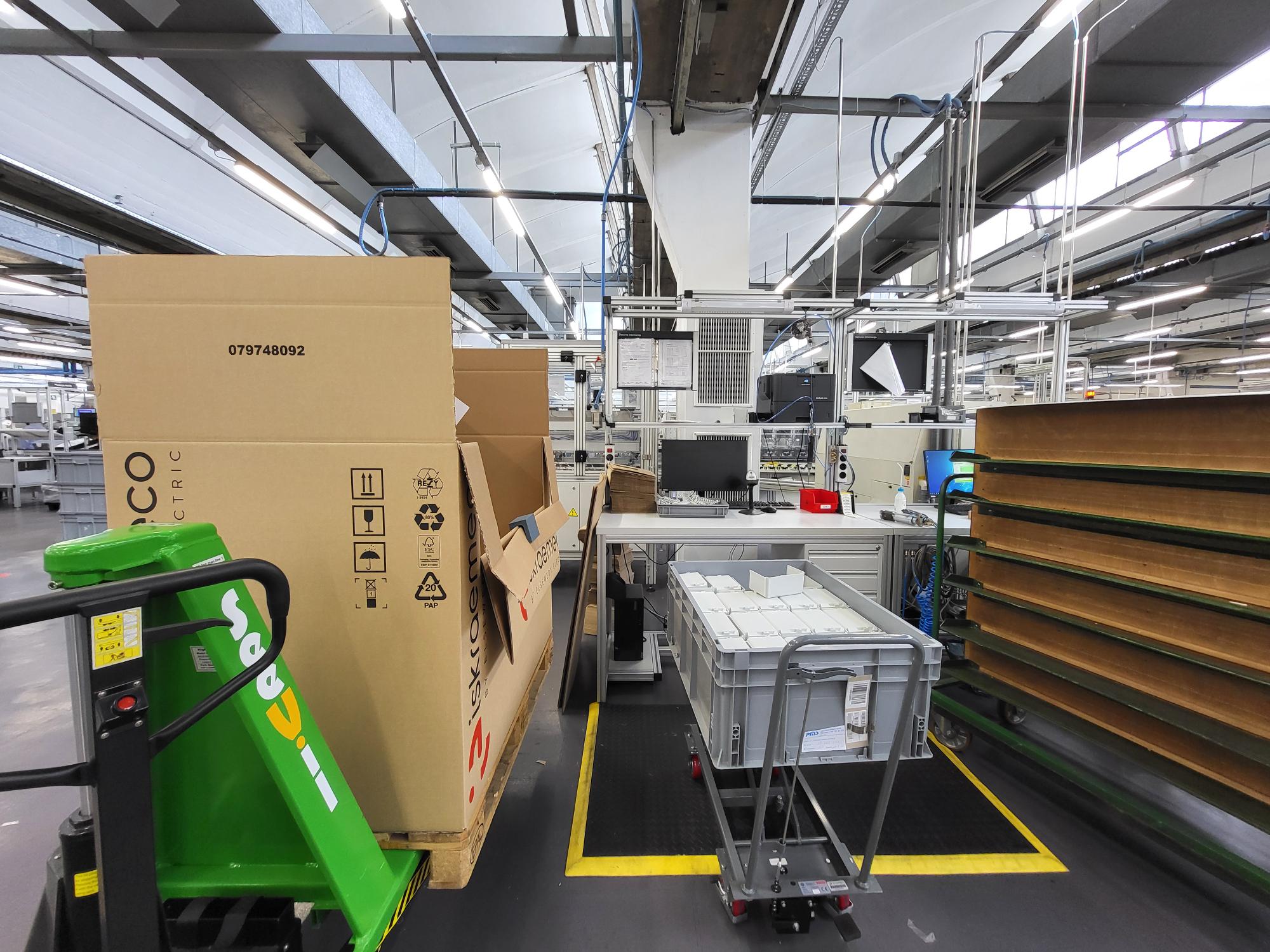
Transport
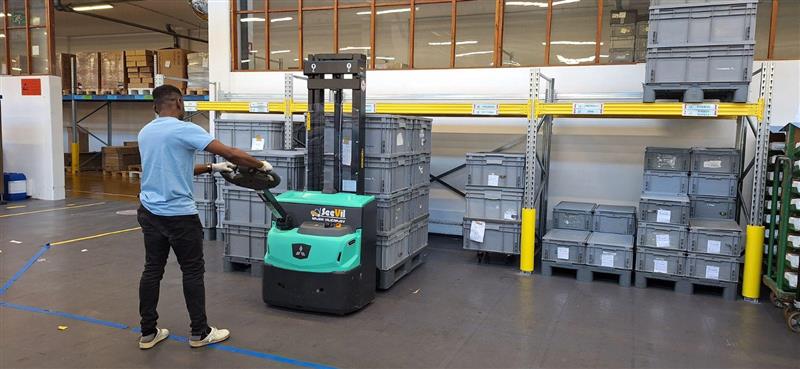
Inventory
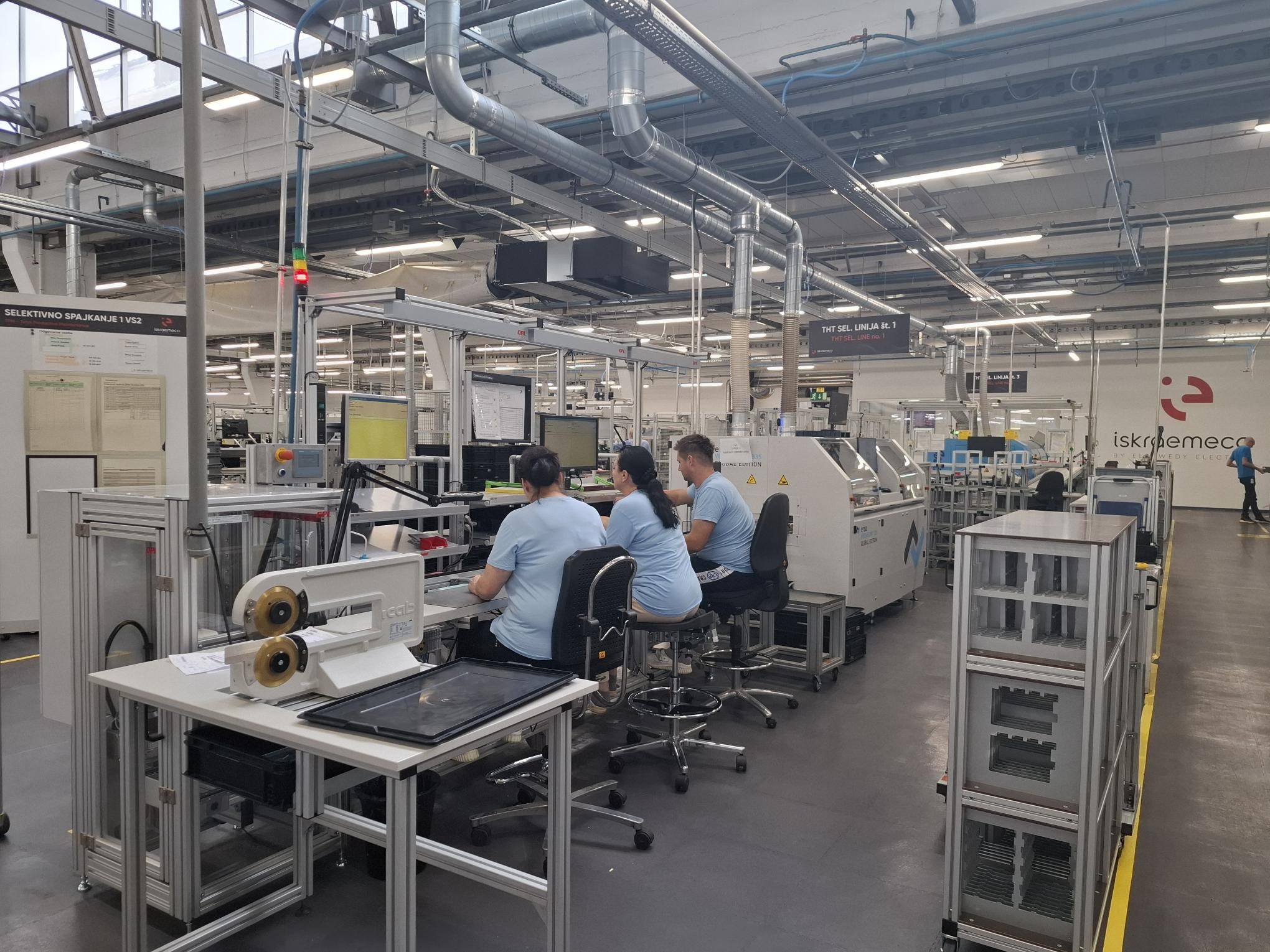
Motion
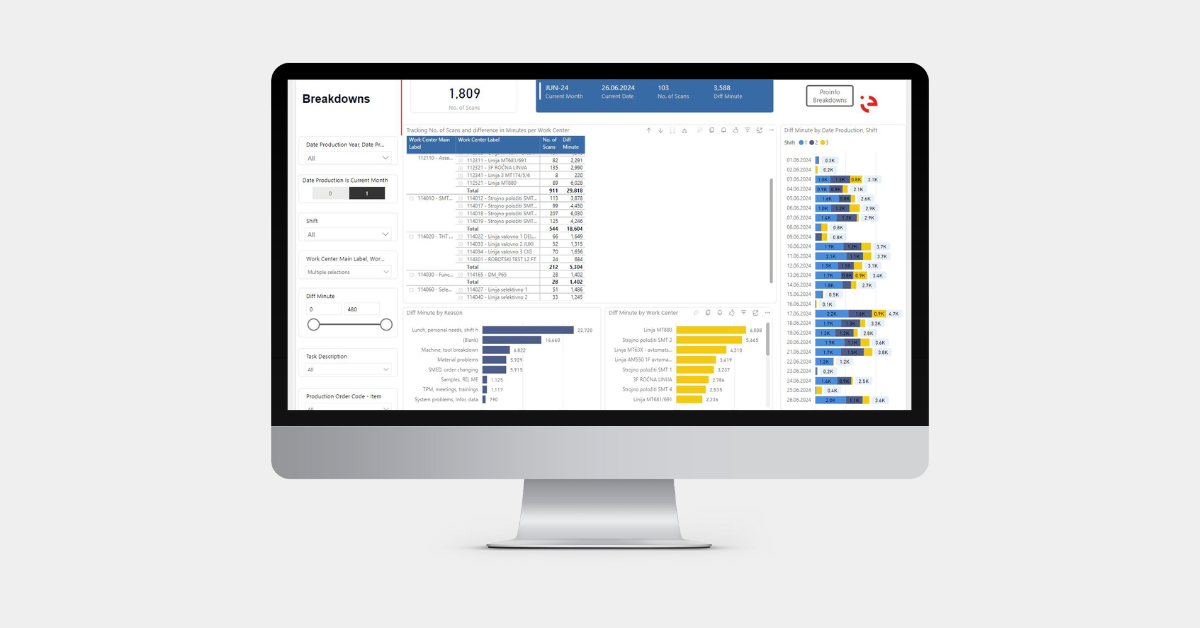
Waiting
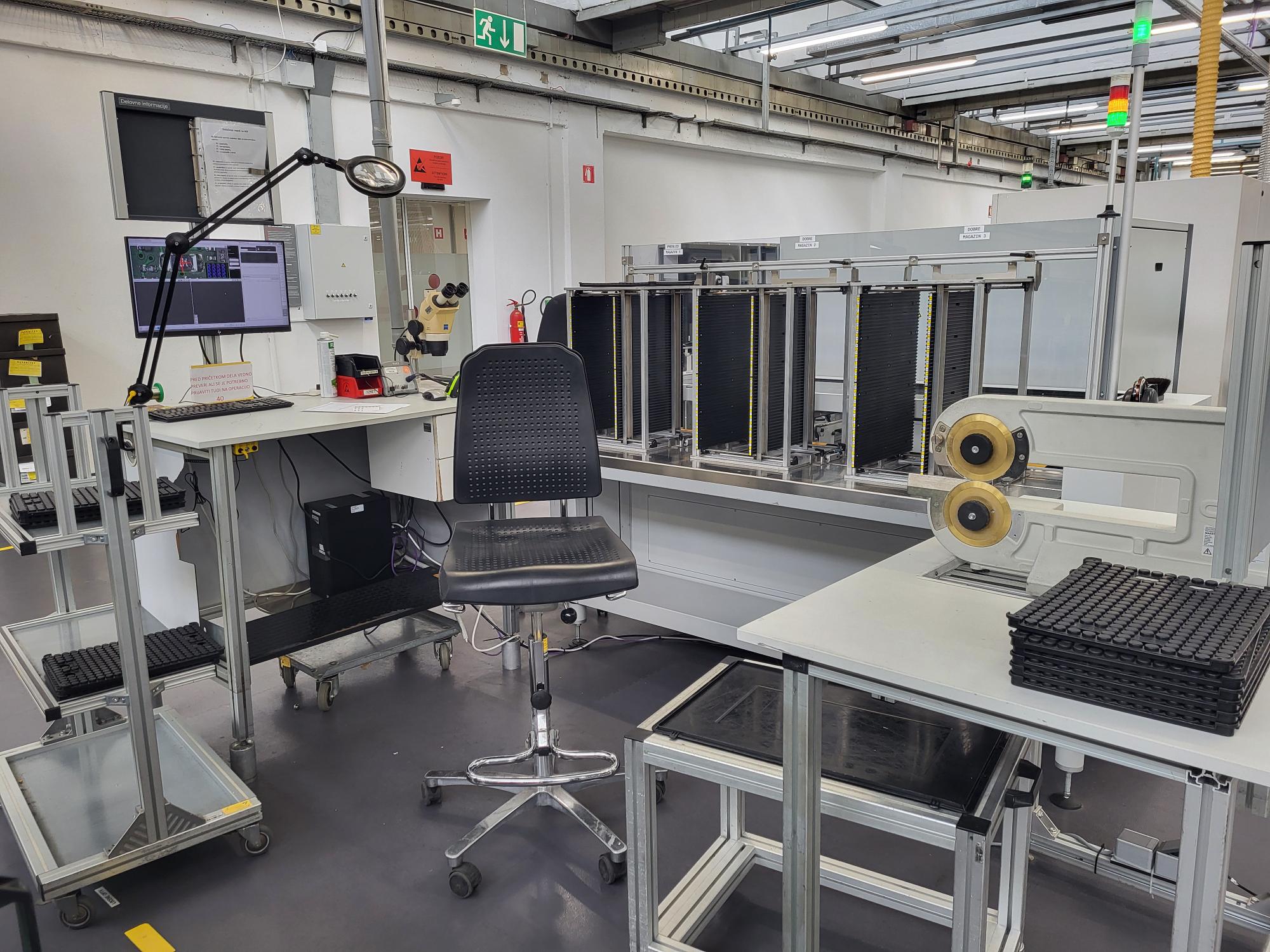
Unnecessary workflows
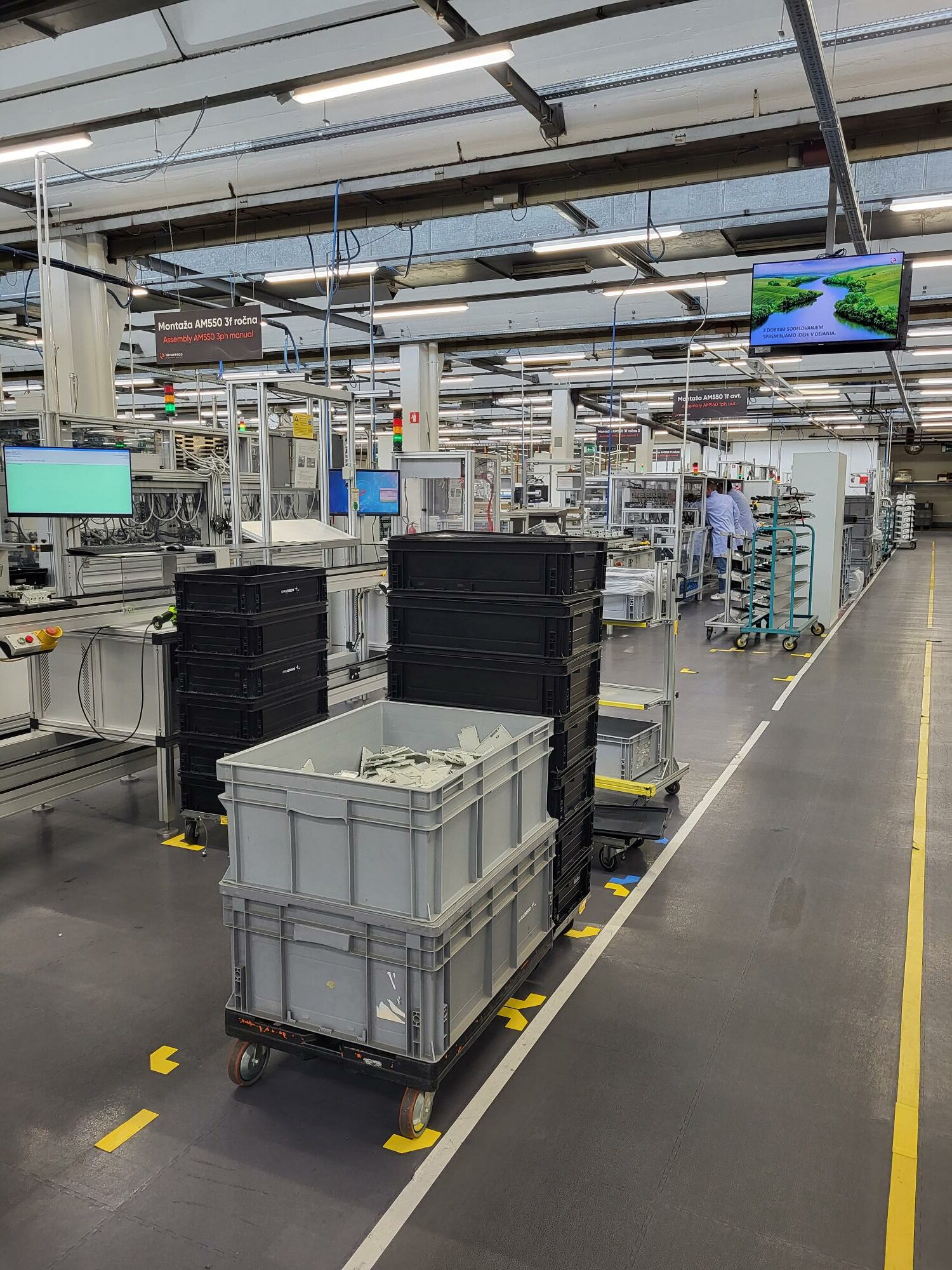
Overproduction
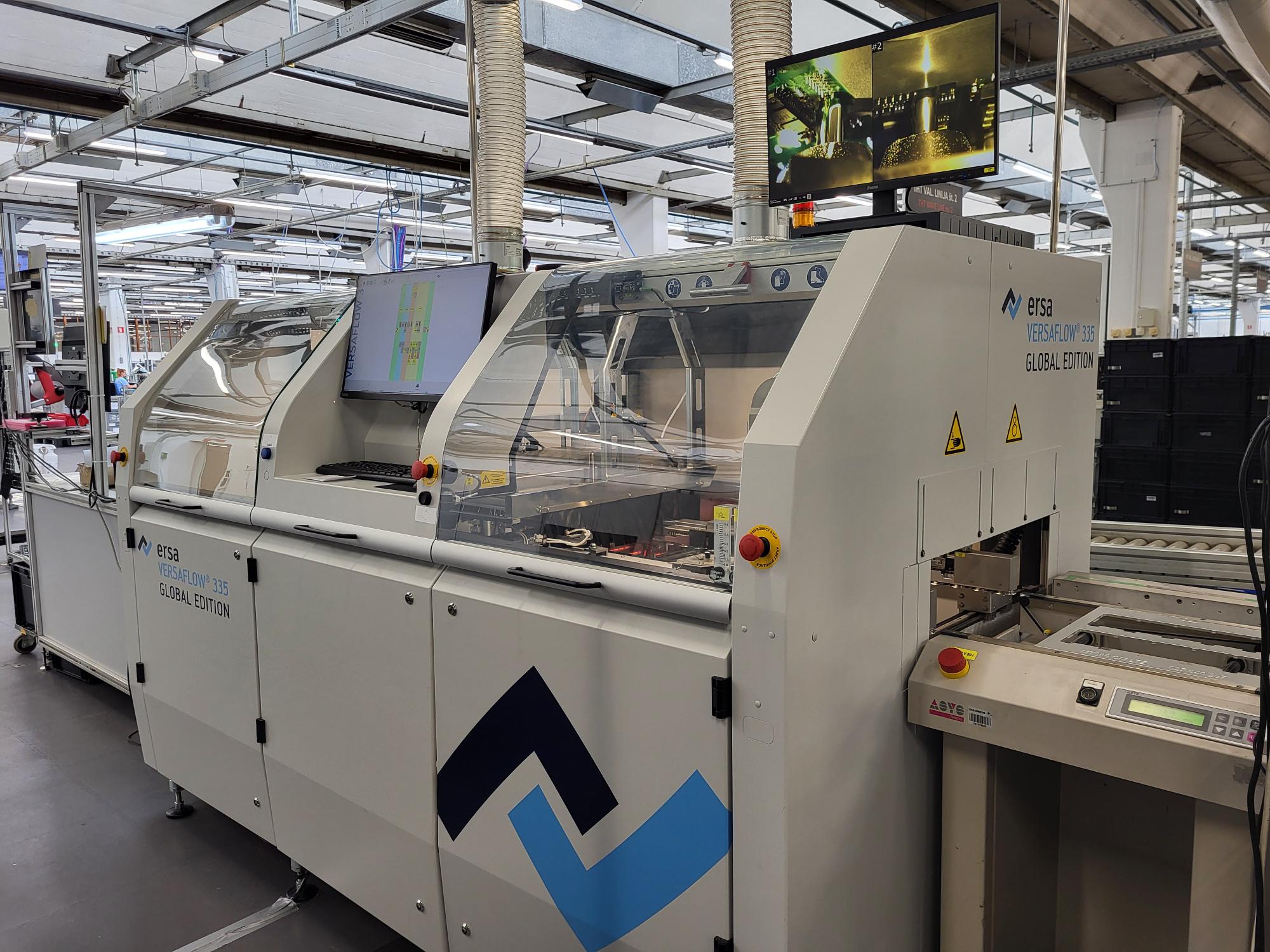
Defects
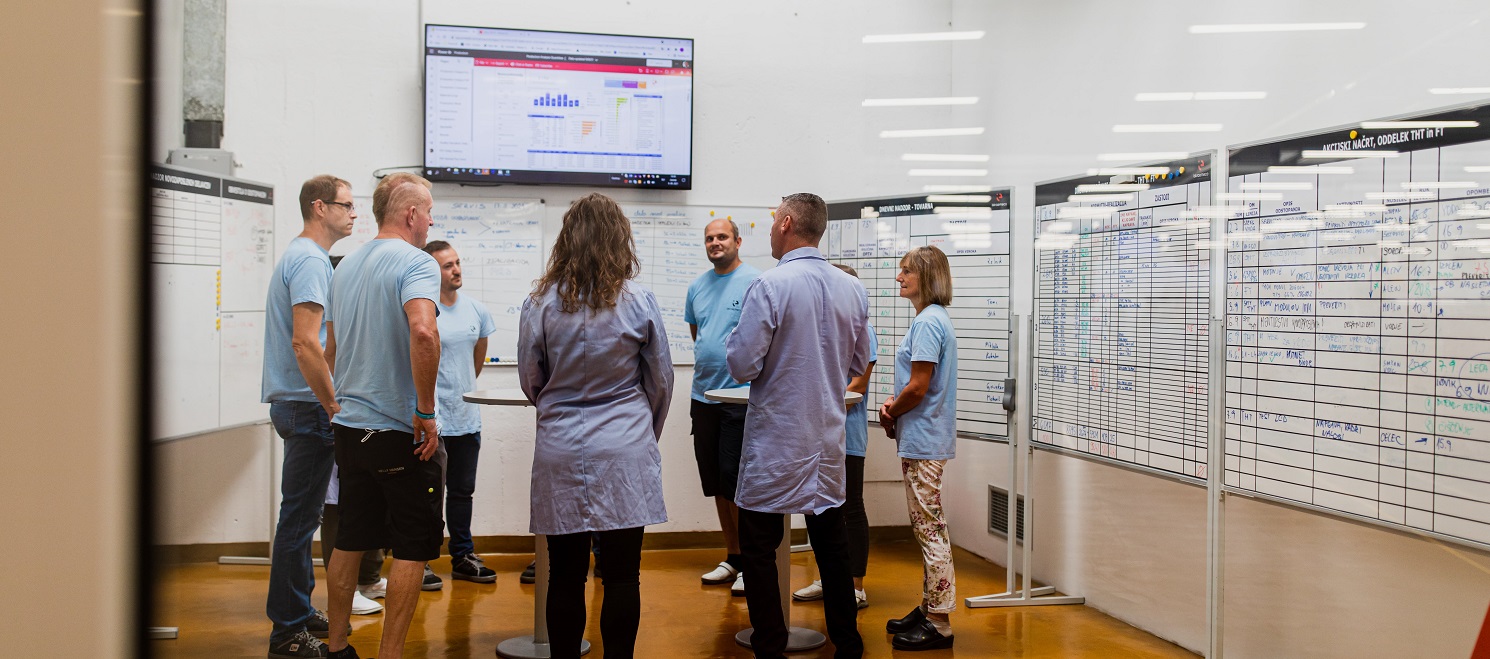
Skills
What are the benefits of our improvements?
We have all been actively involved in finding new solutions and eliminating bottlenecks in our processes. Collaboration, innovation and a constant desire to learn have enabled us to achieve significant results:
- Increased efficiency: By reducing losses, we have increased our production efficiency and therefore reduced costs.
- Improved quality: Better process control and reduced defects have led to improved product quality.
- Greater customer satisfaction: Faster delivery times and better product quality have increased customer satisfaction.
- Better working environment: Optimizing workstations and reducing physical strain have led to a better working environment for our employees.
- Increased competitiveness: Continuous improvements have made us more competitive in the market.
At Iskraemeco, we believe that continuous improvement is the key to success. By implementing various measures, we have significantly reduced production losses and increased our efficiency. However, we are aware that this is an ongoing process. Therefore, we will continue to look for new ways to improve our processes and remain competitive in the market.